At OpenUC2, we believe that open-source technology is the future of scientific innovation. By making our designs, code, and processes accessible to everyone, we foster a global community to contribute, experiment, and expand the possibilities of modular microscopy. Our mission is to provide a platform where both researchers and enthusiasts can collaborate to push the boundaries of science. Open-source is not just a methodology. The center: The Cube. But how can we make the cube, talk?
Cube is Key
Recently, we asked our community for feedback on the next version of our modular cubes. One of the top requests was the integration of electronics into the cubes, enabling users to connect and control components such as motors, LEDs, and sensors. The feedback inspired us to integrate the I2C bus into the cubes. Here is how we did it.
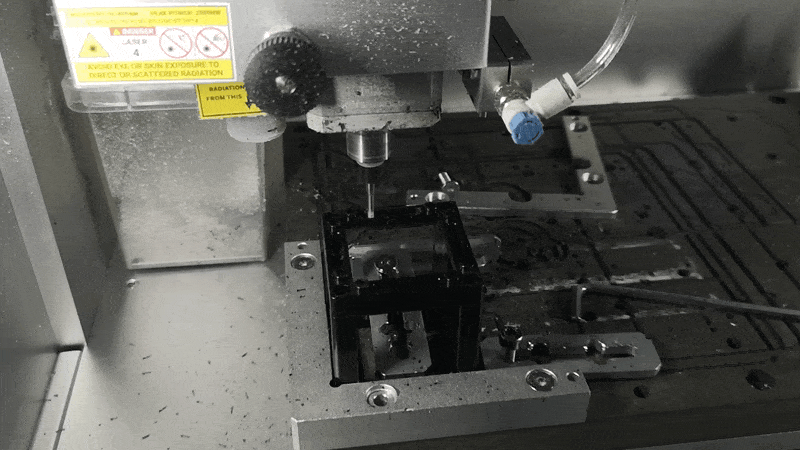
The result is an exciting new feature: a bus system integrated into the cubes, allowing electronic components to communicate across the entire setup. We’ve chosen a robust, industry-standard protocol that operates with just four wires (I2C) —power, ground, data, and clock—enabling simple and efficient communication between the cubes. This setup not only simplifies the control of motors and sensors but also relieves the CPU on the mainboard, allowing it to focus on higher-level tasks, such as interfacing with external controllers or managing WiFi communication.
Learning from Google’s Project Ara: Modular, but Better (and actually available..)
Our vision is inspired by the crazy idea to make smarpthones more modualar and sustainable – called Google’s Project Ara. While the Ara phone ultimately did not succeed, it offered valuable lessons on how modularity could revolutionize technology—if done correctly. One key takeaway was that robust physical connections are crucial for modular systems to work seamlessly.
That’s where Pogopins come in (kinda..). These tiny spring-loaded pins offer a reliable solution for connecting modular electronic components, even when there are small imperfections in alignment. In our cube system, Pogopins ensure stable electrical connections, allowing modules to “snap” together and communicate (hopefully).
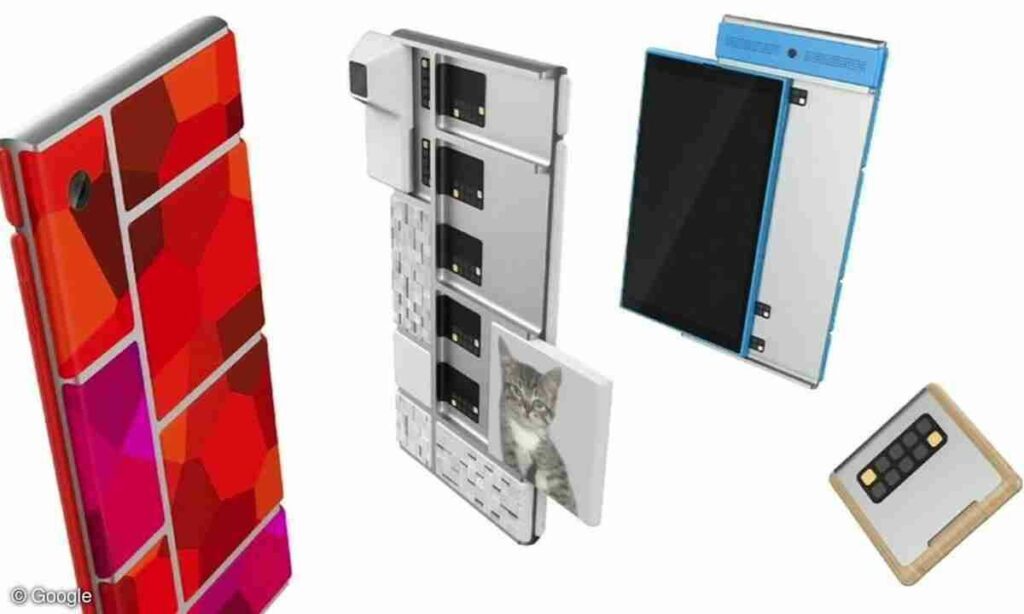
Crafting a Modular Electronics System
With the idea of using Pogopins for connectivity, we set out to integrate them into our modular cube design. The challenge was to create a system where cubes could communicate and share power efficiently, while still maintaining the flexibility that defines OpenUC2.
We started by designing a simple 12V power and messaging system. The cubes are all connected to the same signals (power, ground, data, clock) that allows them to share both electrical signals and control commands.
For the physical integration, we used our Bambu Lab 3D (P1P) printers and Makera Carvera CNC machine to modify our existing injection-molded cube design. This allowed us to create small slots within the cubes where printed circuit boards (PCBs) could be inserted. These PCBs house the Pogopins, which then connect the electronics in each cube to the overall bus system. The result is a smooth, modular integration of electronics into the cubes, enabling the quick swapping and control of different modules without the need for complex wiring.
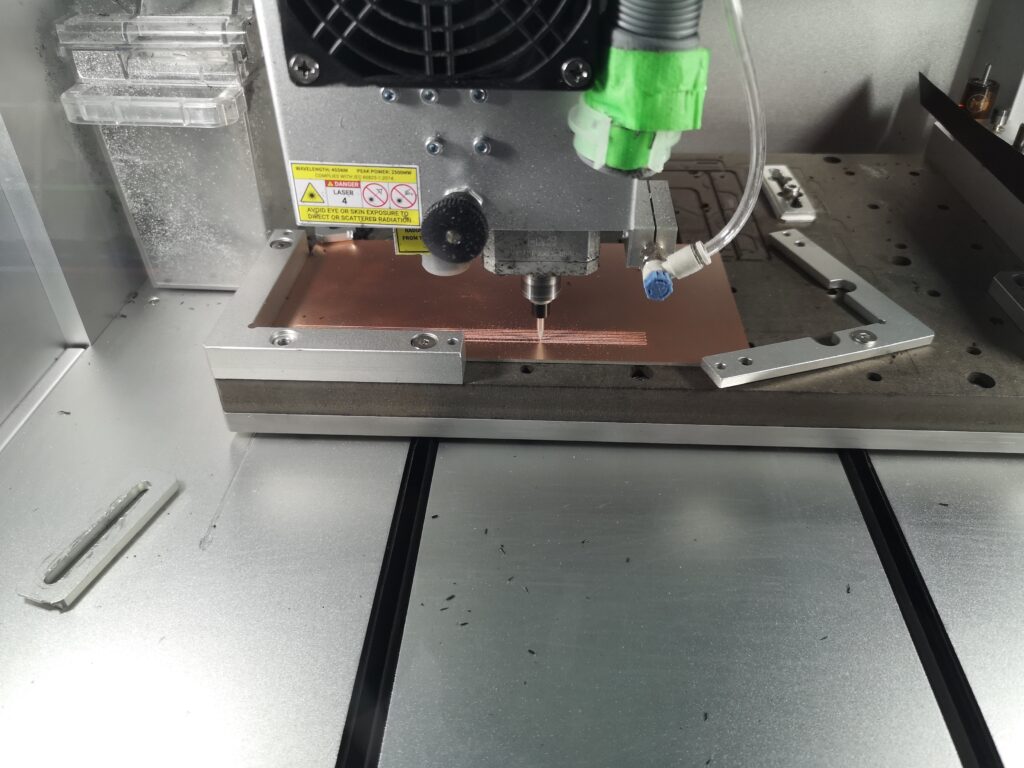
Rapid Prototyping: From idea to instrument
Our prototyping journey involved several steps, starting with a custom PCB design. We used open-source tools like KiCad to draw up a simple four-wire circuit, which we then converted to G-code using EasyCAM. The PCB was then milled using our Carvera machine, ensuring that the connections between the Pogopins and the rest of the electronics were solid.
In the current prototype, we used standard 2mm diameter Pogopins arranged in a row-like pattern. These pins are soldered to the PCB and extend out of the cube’s surface, ready to connect with the base plate. The base plate itself houses the main PCB, which distributes power and control signals to the cubes through these Pogopins. This system allows for three cubes to be connected in series, with one cube acting as the master controller, communicating with the other modules through the signal bus.
The beauty of this system lies in its simplicity: by using standard components and open-source design tools, we’ve created a flexible, scalable solution that can be easily adapted and improved by anyone in the community. From this we can easily build a more-robust longlasting system ready for production.
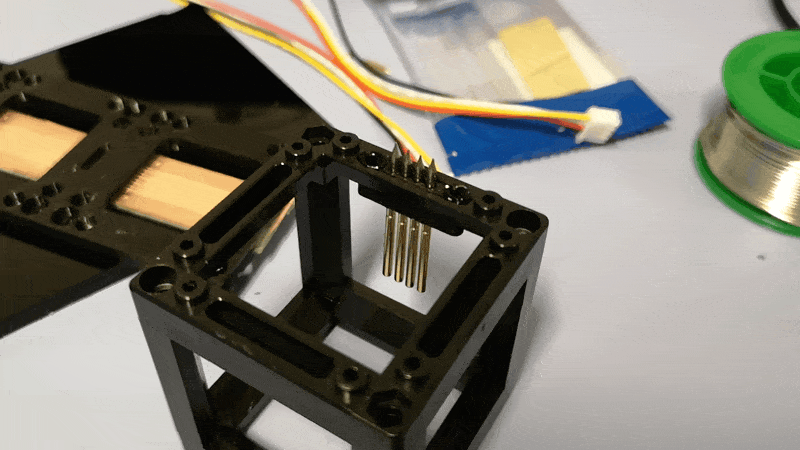
A smart base
The herin created “smart base” plate can route control signals to various cubes, making it easier to swap out components on the fly and configure arbitrary complicated systems. This prepares our cubes to integrate in smart microscopy frameworks. At the core of this evolution is the UC2-ESP32 firmware, which continues to handle the heavy lifting of communication and control in our setups.
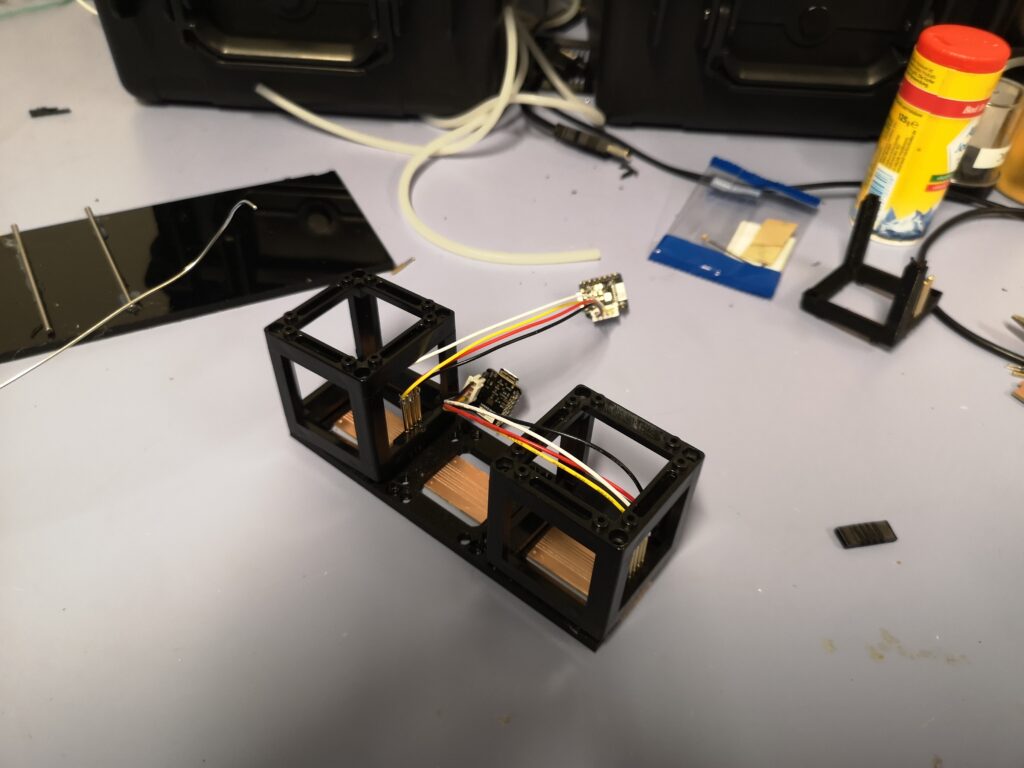
Share Your Ideas
We’re eager to hear from you—our community—about what features you’d like to see in the next iteration of our modular electronics system. Do you have ideas for new sensors, motors, or controllers that could be integrated into the cubes? Let us know!
Feel free to reach out with suggestions or ideas, and let’s keep pushing the boundaries of what’s possible! Watch out at www.openuc2.discourse.group